Fabrication and layout of surface pipelines in mining operations can require substantial labor, time and costs. This is often due to location – generally in remote areas where terrain makes laying above-ground lines a particular challenge, according to German pipe manufacturer Rädlinger primus line GmbH.
“To keep mining operations running, water and other process media must be transported through a remote and rugged terrain, where the weather is often times extreme, the access is limited, and the risks are high. It is essential to have a reliable and durable pipelines system that can handle the challenges and deliver the targeted results,” Heiko Manzke, director–Australia and New Zealand for Rädlinger, explained.
That’s why Rädlinger developed the Primus Line Overland Piping system, designed with features that can considerably reduce the resource outlay. Key system features include a unique aramid-reinforced and composite liner along with leak-free connectors that the company claims makes it more durable and flexible than other systems.
“The lining of the flexible pipelines consists of thermoplastic polyurethane (TPU), a very durable polymer. Its outer layer, also made of TPU, offers maximum protection from UV light and abrasion as well as the required flexibility for repeated installations and coiling of the reusable system,” said Manzke.
Typically, mine piping systems must resist abrasion, impact, UV light and other environmental stresses that affect the outer layers of the pipe, while internally they must be able to cope with abrasive materials and harsh chemicals. The Primus Line Overland Piping system offers a three-layer structure designed to meet these challenges and improve durability. The outer TPU layer protects against external influences, and the aramid-reinforced middle layer ensures flexibility of the liner, making it reusable and bendable. A third, inner layer provides strong chemical resistance that can withstand contact with highly corrosive hydrocarbon compounds. “This design differentiates the solution from other systems resulting in a generally longer service life and ensuring a successful operation without leakage and environmental damage,” Manzke explained.
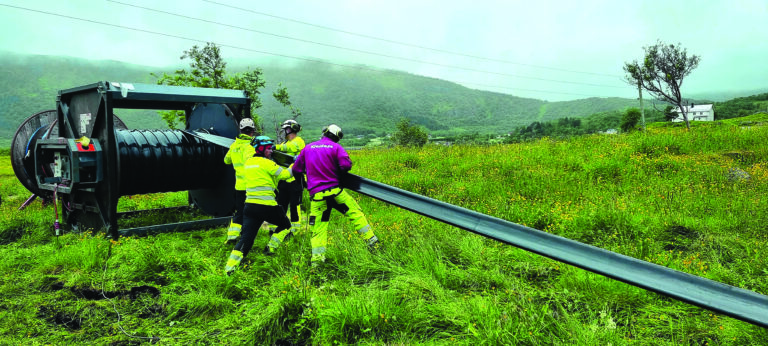
According to the company, the choice of aramid as a core material was no coincidence: It’s ten times stronger than steel and twice that of glass fibre or nylon. The aramid fabric therefore makes Primus Line flexible and, in combination with the TPU layers, safe at the same time. “Based on the standard API 15LF, the burst pressure is at least two and a half times higher than the permissible operating pressure,” Manzke noted. In addition, this fabric provides increased tensile strength that allows for very high operating pressures.
The system, according to the company, offers ease of installation without need of heavy equipment or large crews. “Construction of 3.7 miles (6 km) of pipelines only takes about one to two days with a crew of three to four people. In comparison, it takes about 25 to 30 days to lay the same distance with a crew of four to six people using HDPE pipes,” said Manzke. Once on site, installation requires only a mini-excavator or winch and basic hand tools. Removing the piping is similarly convenient, as it can be coiled flat on special transport reels that are provided to the customer. This approach can minimize both logistical costs and the environmental impact associated with transportation, according to Rädlinger.
Specially developed high-pressure end fittings with flanges or quick couplers compatible with Victaulic notched products are used to link various flexible sections, allowing quick, easy installation for a wide range of layouts. They can also be connected to pumps or other pipeline assets and do not require hot work such as welding or butt fusion for installation. In addition, the overall number of necessary joints for the pipeline infrastructure is smaller: Fewer joints mean less weak points. “We provide installation lengths of 3,300 ft (1,000 m) and more to reduce the number of necessary joints, especially when compared to HDPE pipe, thus making this solution particularly safe to use and operate,” explained Manzke.
In order to minimize operating costs, the company said that in addition to its simpler pipelaying approach and reusability, storage facilities can be smaller; depending on the diameter, up to 13,000 ft (4,000 m) of the flexible pipe can fit on one transport reel. In comparison, storage of HDPE pipe requires up to ten times more space, according to the company.