A selection of impressive bridge projects from around the world, revealing the wide range of techniques and equipment used to build them.
Tower cranes, fast erectors, lattice boom crawlers, telecrawlers, SPMTs, winches, jacks, RoRo ramps, shear legs and barges – in the following six case studies you’ll see all this equipment, and more, being utilised for the purpose of building various bridges around the world.
Despite the wide range of techniques and equipment employed, however, there are common threads underpinning this essential area of infrastructure construction: namely the importance of innovative thinking, detailed planning, and maintaining a flexible approach…
Who: Sarens / Smulders.
What: Transport and installation of two bridge sections of the Clyde Waterfront and Renfrew Riverside swing bridge.
Where: Glasgow, UK.
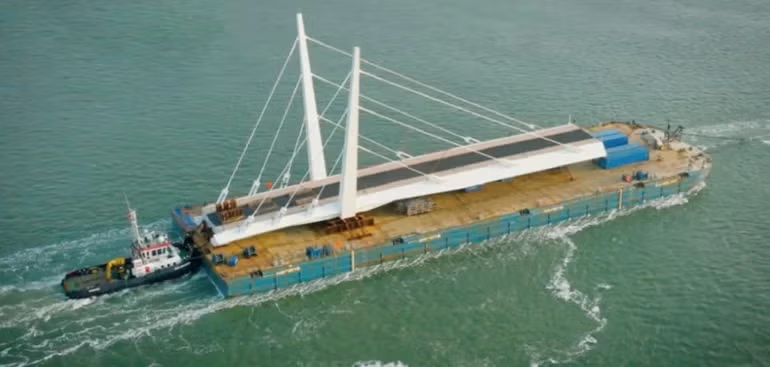
Sarens, contracted by international construction company Smulders, played a crucial role in the transport and installation of two sections of a bridge over the river Clyde, Scotland.
One bridge section was constructed by Hollandia Infra in Rotterdam, Netherlands. The other was constructed by Smulders in Flushing, Netherlands.
Both bridge sections had to be transported and installed in Glasgow, the UK.
To undertake this crucial project, Sarens studied the site conditions in Rotterdam, Flushing, and Glasgow and decided to deploy:
- Sarens’ barge Caroline
- 26 ballast pumps (600T/h)
- six hydraulic winches (50 tonne)
- SPMTs in various configurations (6×10 axle-lines, 2×16 axle-lines, 2×12 axle-lines)
- RoRo ramps of 2.75m, 5.8m, and 9m. Some equipment was shipped on the barge, while the rest was transported by road.
Each bridge section weighed about 1600 tonnes and measured 92m in length, 18m in width, and 38m in height. Due to site-specific requirements in Rotterdam and Flushing, different SPMT configurations were used. In Rotterdam, limited space and ground pressure led to a setup of 6×10 axle-lines, while in Flushing, 4×16 axle-lines were required due to ground pressure limitations.
Extensive ballasting was necessary in both Glasgow and Flushing to maintain the correct draft and trim, compensating for tide and load variations during operations.
The south bridge in Rotterdam was transported to the quayside using six ten-axle SPMTs, lifted by three shear legs, and loaded onto Sarens’ barge Caroline. After securing the load, the barge was towed to Glasgow, where pre-assembled SPMTs (two sets of 12- axle units) were used to move the bridge to its final position on temporary jacks.
The north bridge in Flushing, Netherlands, followed a slightly different process. It was transported to the quayside using 32-axle SPMTs, driven onto the barge during a load-out operation, and transported to Glasgow. The installation sequence in Glasgow mirrored that of the south bridge.
The project involved a crew of 14 individuals, working in double shifts to minimise the barge’s presence in the river navigation channel in Glasgow. Due to limited water depth, a ramp structure on piles bridged the gap between the barge and quay, with the longest gap being around 18 metres.
Who: Mammoet / McConnell Dowell.
What: Accelerated Bridge Construction (ABC) approach to installing an elevated rail bridge over a busy road in a built-up area whilst minimising traffic disruption.
Where: Melbourne, Australia.
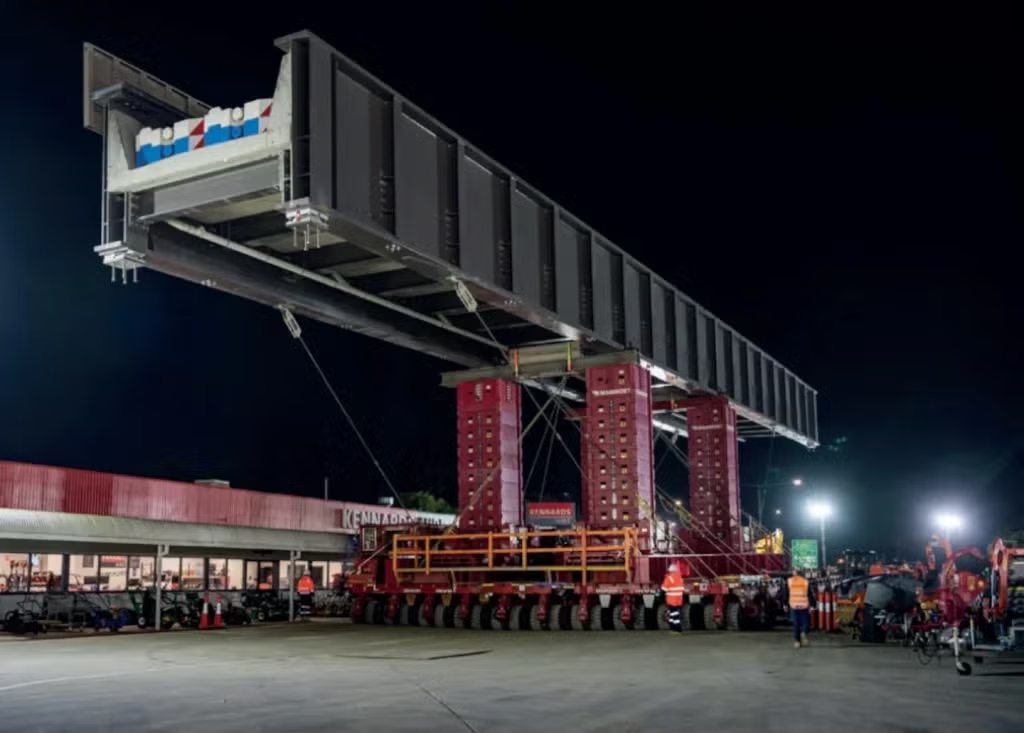
Contractor McConnell Dowell commissioned Mammoet to fabricate, transport, and instal an elevated rail bridge over a busy road in an urban part of Melbourne.
For this Mammoet utilised SPMTs in combination with its Enerpac JS500 jacking system. First, the SPMTs raised the bridge sections from 1.5m to 4.2m high to prepare for the main jacking operation. Next, with SPMTs reconfigured and JS500 jacking units secured, the team jacked up the bridge to a transport height of 9m, ensuring clearance over street furniture and other obstacles.
After navigating through the urban area the bridge sections were then jacked down onto their foundations.
According to Mammoet the selected installation methodology not only minimised traffic congestion, but also mitigated the safety risks typical in traditional construction methods.
A video of the project can be seen here
Who: Wolffkran / Porr.
What: Wolff cranes are helping build a 667-metre-long, 90-metre-high bridge over the river Neckar.
Where: Horb, Neckar Valley, Baden-Württemberg, Germany.
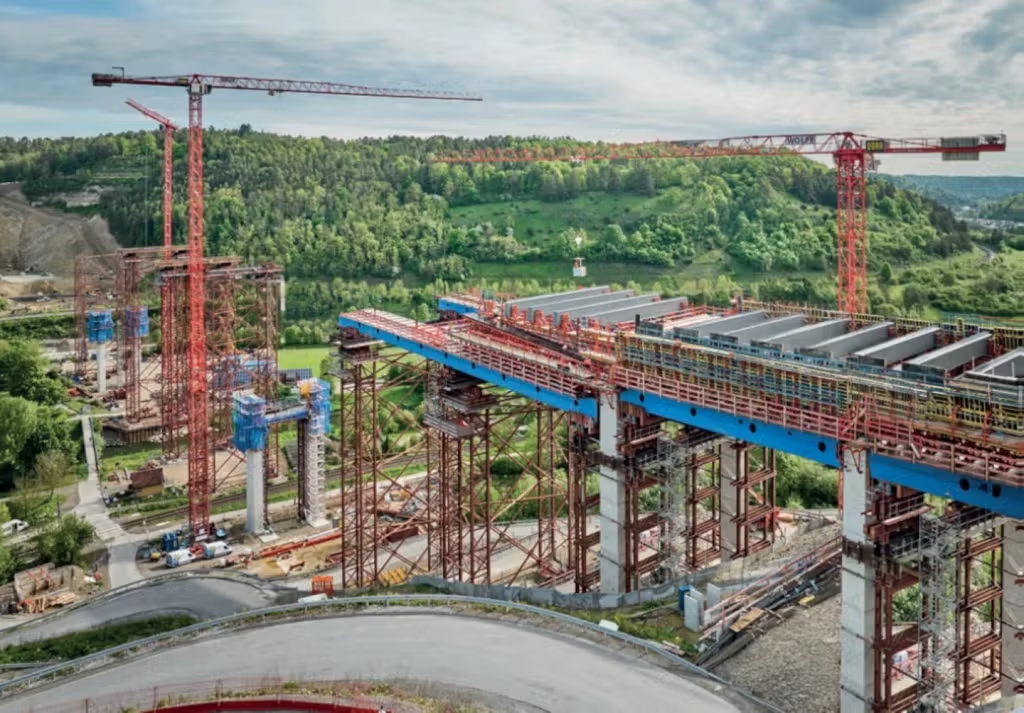
German construction company Porr is utilising five Wolff tower cranes to build the bridge across the river Neckar, a rail line, and a cycle path – meaning space is tight on the job site. Two of the five tower cranes are Wolff 7534.16 Clear models. They are freestanding, operating at around 100 metres high.
With 75-metre jibs, they are lifting a maximum of 16.5 tonnes, and 3.4 tonnes at the top (four-strand operation). “This is normally not possible with a freestanding crane,” explains Wolfgang Kavelius, sales manager at Wolffkran. “But the special design of the bridge piers meant that no tie-ins could be used, or they would have been disproportionately complex and expensive.”
To ensure the necessary stability, the towers were assembled using three different tower elements. The lower third of the towers is formed by the TV 33 tower elements with a side length of 3.3 metres. Above this is a transition area composed of tower sections with side lengths of 2.5 metres. And on the upper half of the tower are 2×2-metre tower sections (TV 20). “This specialised structure makes it possible to limit the maximum tower deformation to well under two metres, thus allowing the cranes to be operated safely as freestanding units,” explains Peter Hegenbart, head of sales project engineering at Wolffkran.
Who: Liebherr / Implenia / Plauen Stahl Technologie / ZSB Zwickauer Sonderstahlbau.
What: Liebherr cranes are helping replace the Rader High Bridge, Germany’s second-longest steel road bridge.
Where: Schleswig-Holstein, Germany (where the A7 motorway crosses the Kiel Canal).
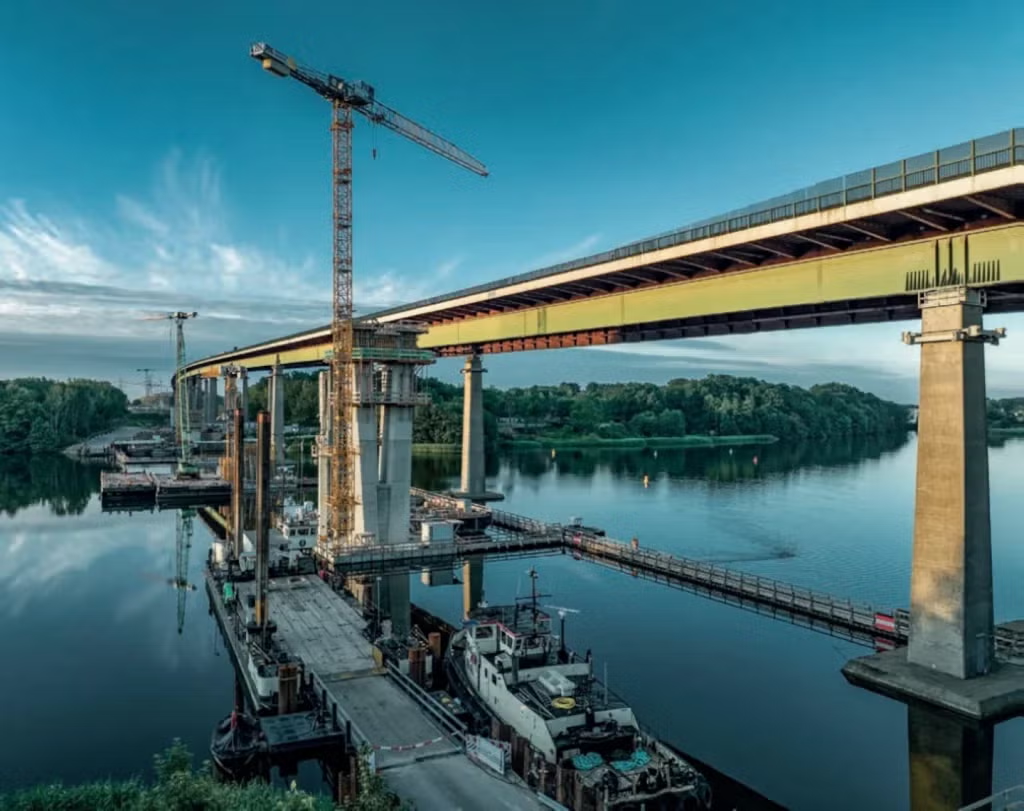
18 Liebherr cranes are helping replace and widen the Rader High Bridge in one of Germany’s largest bridge modernisation projects. It is being carried out by a consortium headed by Swiss construction company Implenia, together with two Saxony-based companies – Plauen Stahl Technologie and ZSB Zwickauer Sonderstahlbau.
Specifically, five fast-erecting cranes (two 65 Ks and three 81 Ks) are on site to assist with the foundations while the new bridge piers are being built with the help of six 125 EC-B and seven 150 EC-B flat-top cranes.
The first crane on the site was a 125 EC-B. This was assembled in the waters of Lake Borgstedt, where the crane stood on the first pier’s pile cap secured by foundation anchors. This crane was assembled by a 250-tonne Liebherr LR 1250 crawler crane on a floating platform. The crawler then assembled three further 125 EC-Bs from the floating platform.
A 150 EC-B 8 Litronic started off working on the bridge on the land but, at the end of June 2024, was moved and reassembled in the water with the help of a 220-tonne crawler crane on a floating platform.
Liebherr’s Tower Crane Solutions (TCS) team was involved with the complex planning.
A major challenge lay in the cranes being assembled by the crawler crane on the floating platform. As the permissible hook height of the crawler crane on the floating platform was restricted, the assembly height had to be kept as low as possible. However, a certain tower height was also necessary so that the cranes could be climbed. Various options and tower systems were therefore investigated in the run-up to the project in order to find the best solution.
The TCS team was also involved with determining the configuration of the tower combinations to prevent the towers from colliding with the newly erected bridge piers.
Who: Lane Construction Corp/ South Carolina Department of Transportation / Link-Belt Cranes.
What: Two Link-Belt telescopic crawler cranes are constructing two bridges over a river to replace preexisting overpasses along Interstate 20 in South Carolina, USA.
Where: Wateree River, Kershaw County, South Carolina.
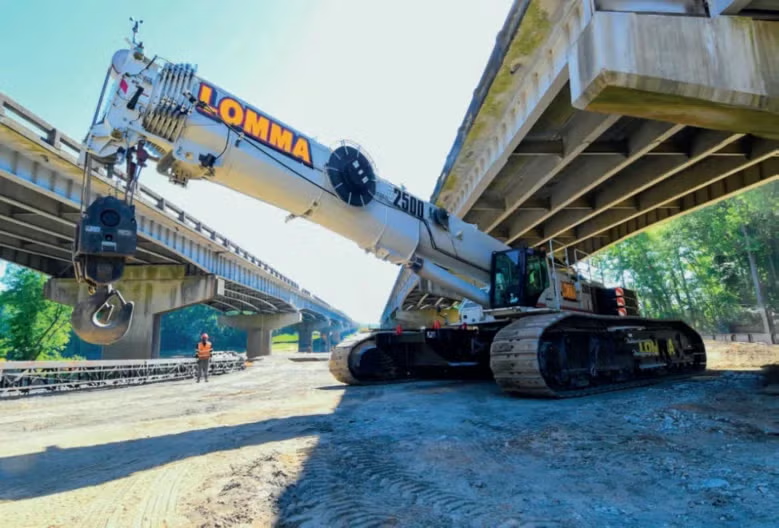
North Carolina-headquartered construction company Lane Construction Corporation is utilising two Link-Belt TCC-2500 telecrawlers to build two bridges over the Wateree River in South Carolina. The bridges will replace two preexisting overpasses along Interstate 20 as part of a bridge rehabilitation project for the South Carolina Department of Transportation.
Renting the TCC-2500s from Lomma Crane & Rigging, of Bridgeville, Pennsylvania, Lane first used the TCC-2500s to drive piling to build temporary trestles on both sides of the river. As the river is a navigable waterway, and requires maintained access through its middle, the Lane work crew is using the TCC-2500s concurrently, one on each trestle, to begin foundation work for the replacement bridges.
Although a traditional lattice boom crane was used to start the project, Lane project director Eric Pruemer soon realised it was not optimised for the tight job site, stating it was constantly in the way and difficult to move efficiently.
He says the TCC-2500s’ manoeuvrability was exactly what was needed to do the job right.
“These allow us to easily go underneath the bridge back and forth to facilitate work on both the outside and the median of this bridge,” he said. “The cranes are very sleek, and they work very well.”
Pruemer notes that the cranes’ ability to quickly retract and extend their booms mean they can travel under each bridge easily and work on either side when driving the steel tubular pile needed to construct bracing for the existing bridges throughout the demolition process, saving the crew time and money.
“Without that, it would’ve been a half day to a day of dismantling the crane, moving it over, and then reassembling it,” Pruemer says.
The TCC-2500s’ ability to work and manoeuvre efficiently in close quarters made the difference to Lane, says Link- Belt and it is now using them exclusively for the rest of the job, as the company needs to keep road and water traffic open throughout the duration of the project.
The cranes are likely be on-site for between six to eight months.
A video of the project can be seen here
Who: Vernazza Autogru / Fincantieri / Tadano.
What: Two lattice boom crawler cranes used for tandem lift of bridge sections over road and rail lines at a busy port.
Where: Porto di Prà, Italy.
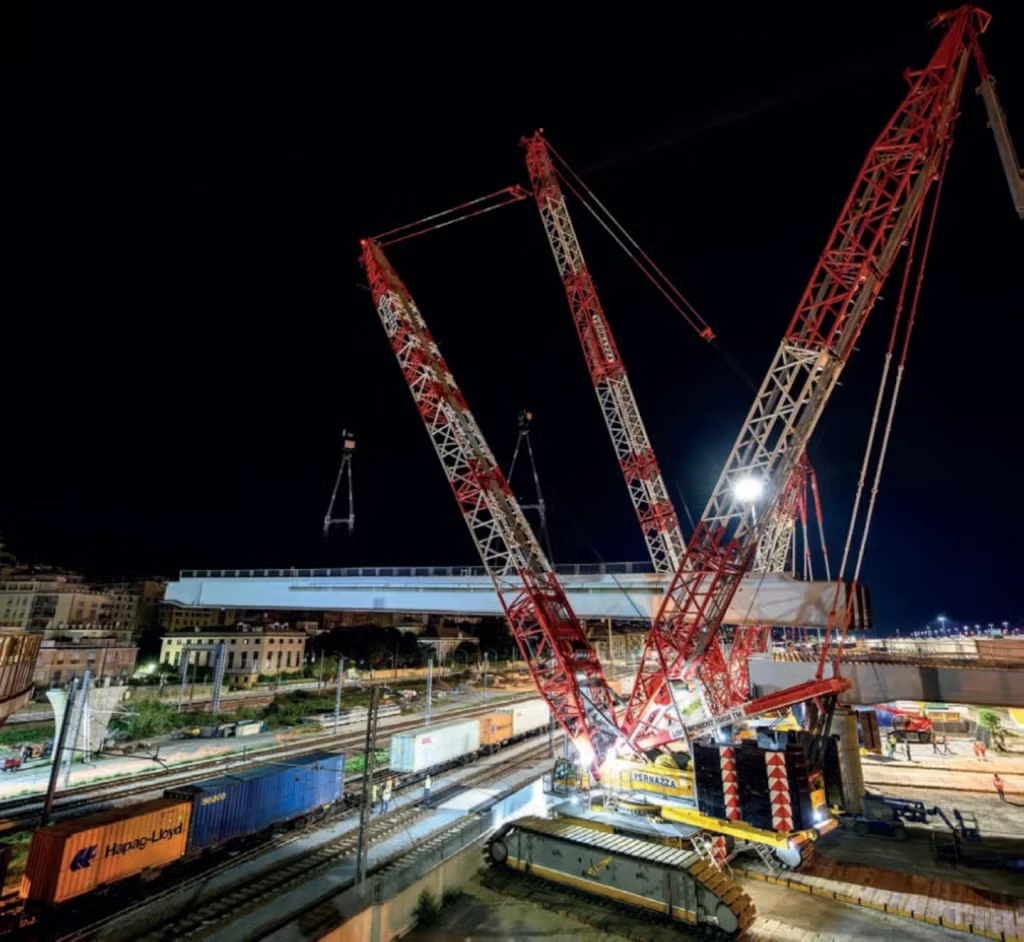
Italian crane service provider Vernazza Autogru was commissioned by shipbuilder Fincantieri to lift two bridge sections, with a weight of 500 and 290 tonnes, for a bridge structure at the Porto di Prà shipyard.
The loads comprised bridge sections made of steel girders with a concrete deck on top. The loads had to be lifted and then moved, whilst in the air, onto pillars. For this Vernazza Autogru selected to use its Tadano CC 68.1250-1 and CC 38.650-1 crawler cranes.
A tandem lift was used for the 500-tonne bridge section, while the CC 68.1250-1 lifted the 290-tonne section on its own. The CC 68.1250-1 was set up with an SSL configuration, a 72-metre boom, and 450 tonnes of Superlift counterweight; the CC 38.650-1 was also set up with an SSL configuration and a boom of the same length, but 325 tonnes of Superlift counterweight.
The two cranes lifted and moved the 500-tonne section together at a radius of 50 metres and a height of seven metres, while the CC 68.1250-1 put the 290-tonne section in place at a radius of 41 metres and a height of nine metres.
The lifts were over existing bridges, the Genoa-Ventimiglia railway line and a busy road – so needed to be conducted as quickly as possible to minimise disruption.
From planning to completion the Vernazza team was on-site for a total of four months and the job went smoothly.