Wear parts are often overlooked or taken for granted when it comes to their role in ensuring the sustainability and safety of mining operations. They are the frontline defence against abrasion and corrosion and, if they fail, the consequences can be catastrophic from an environmental, safety and financial perspective. Conversely, when wear parts perform well, they can provide miners with the predictability and reliability that allows them to focus on improving throughput and increasing production.
For example, when Weir lines large, expensive capital equipment, like flotation cells and thickeners, with LINATEX® premium rubber, the customer typically gets between 10-15 years of service life out of that lining. If the life of mine (LOM) is, say, 50 years, then the miner might only have to replace that lining three or four times.
In addition to the operational benefits, a longer lasting product means less waste is generated.
But in order for a product to be truly environmentally-friendly, sustainability needs to be built into its lifecycle. Take LINATEX® rubber as a case in point. It’s 95% natural, high-quality latex and the manufacturing process, which uses a unique liquid compounding phase, ensures that it remains as close as possible to how nature made it.
The unique compounding process of retains the long molecular chains of natural rubber, ensuring the unmatched abrasion resistance. While its formula and the proprietary process have remained unchanged for 100 years, the continuous equipment modernisation and future-proofing makes LINATEX® the most sustainably manufactured rubber on the market.
Weir uses microwave energy to dry its unique rubber, which is a more environmentally-friendly method. The manufacturing processes produce very little effluent with no waste and uses less power to compared to standard rubber production.
Weir has also implemented a number of sustainability initiatives at its Malaysian facility – the sole manufacturer of LINATEX® rubber – including solar panels, rainwater harvesting and a rubber recycling program.
Wear part selection
In a typical mill circuit, LINATEX® rubber can be used from the discharge of the ball and SAG mills, which then feed the cyclone clusters. The cyclone underflow feeds back to the ball mills, while the overflow feeds the thickeners, tertiary grind areas and flotation. This is the part of the processing plant that requires a product that can withstand wet sliding abrasion – and that’s where LINATEX® rubber excels.
The mill circuit is the heartbeat of the mine; it’s where the mill pumps and cyclones are located and it’s where the Run-of-Mine (ROM) is pushed through the pipes to the concentrator. In other words, maintaining the life of the equipment and pipes and ensuring they stay in service for the longest amount of time possible is vital because failures and shutdowns can cost a significant amount of money.
When it comes to selecting the appropriate thickness of the LINATEX® rubber for specific applications, Weir’s extensive installed base in mines all over the world and in various areas within these mines, ensures that it can select the right product and guarantee its wear life with a high degree of certainty. Crucially, this provides operators with the predictability they need.
Conversely, it’s important not to install a rubber that’s too thick – that reduces the diameter of the pipe, which in turn reduces the throughput and efficiency of the system. It’s about striking a balance between optimal efficiency without compromising the wear life.
Broadly speaking, in areas of the mine where wet sliding abrasion is the norm, like the cyclone feed area, LINATEX® typically lasts twice as long as any other rubber on the market. And, in the right application, compared to, say, metal wear liners, the performance can be exponentially better.

Credit: Weir
Safety, maintenance and monitoring
Better, reliable, more predictable performance also directly correlates with improved on-site safety. If a pipe wears out unbeknownst to the operator, then slurry can leak, creating a line-of-fire hazard and potentially having an adverse effect on the environment. Moreover, there are also slipping hazards associated with having to clean up the site.
Moreover, every time a pipe or piece of equipment has to be removed from its service, the people carrying out the work are at risk.
Weir utilises its NEXT Intelligent Solutions to monitor wear on pipelines, providing operators with increased visibility over wear, enhanced control over performance and greater predictability when scheduling maintenance. A sensor is integrated into the LINATEX® hose or spool and a simple traffic light system enables quick visual identification of its condition. If the hose or spool is less than 50% worn through, then the light displayed is green; if the wear is between 50-70% then it’s yellow and when it’s greater than 75% is flashes red, indicating that it’s time to carry out preventative maintenance.
It was recently installed as part of a solution in Chile, helping the customer recover almost 60,000 tonnes per annum that was being lost because of unplanned downtime and increased maintenance requirements.
Enhanced efficiency, increased production using LINATEX®
At a magnetite plant, the primary ball mill plays a crucial role in achieving target production levels. However, frequent stoppages due to seal-related issues hindered its availability. Every two to three weeks, the maintenance team had to halt the mill for intermediate repairs – adjusting stainless steel rings, water injection lines, or replacing rubber seals – to sustain a maximum campaign duration of three months.
This low availability posed challenges: extending seal lifespan; eliminating water injection; reducing spare parts consumption; enhancing safety during future interventions; and ensuring uninterrupted operations.
Weir identified an improvement opportunity and conducted a 3D scan of the mill seal. The proposed solution featured the LINATEX® rubber mill sealing system, which includes premium rubber seals lasting two to three times longer than conventional ones.
Additionally, the plan addressed misalignment issues by recommending feed spool changes. A static ceramic to rubber seal and an adjustable base for field alignment were introduced to ensure correct concentricity with respect to the mill feed.
Furthermore, the incorporation of NEXT Intelligent Solutions enabled real-time wear monitoring of the interior lining of the ducts. This facilitated efficient job planning, spare parts forecasting and streamlined ordering for the customers maintenance team.
The customer aimed to extend campaign duration to over four months. After implementing the LINATEX® mill sealing system, a post-campaign inspection revealed a dynamic seal lifespan of six months. The system’s components remained in excellent condition during preventative maintenance, resulting in increased equipment availability.
The seal-related issues were resulting in shortfall of over 57,000 metric tonnes of material annually – the LINATEX® solution helped the customer overcome this. Notably, the new solution completely eliminated water consumption associated with the previous seal, contributing to reduced environmental impact and lowering water costs by US$20,000. This pioneering Weir solution, incorporating the LINATEX® mill seal, marked a commitment to efficiency, intelligence, and sustainability – the first of its kind in Latin America.
Taking an integrated, holistic approach
In many ways, LINATEX® typifies Weir’s approach to sustainability. It’s something that it builds into every part of the value chain – starting with responsible sourcing, environmentally-friendly manufacturing and, eventually, delivering a product that helps its customers improve their efficiency and preserve the environment they operating in.
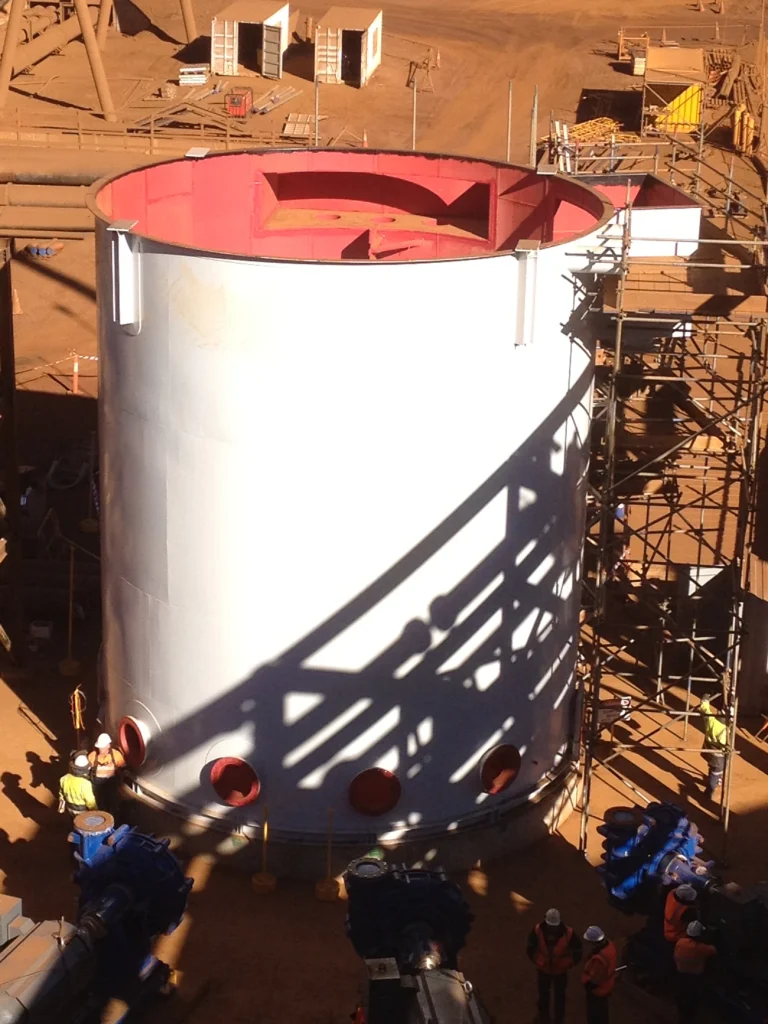
Credit: Weir