Have you ever considered how a continuous miner works? Coal mining operations use these large machines to remove coal reserves from underground coal seams.
The miner consists of a rotating steel drum fitted with tungsten carbide picks that scrape coal from seams.
An optimized continuous miner system moves smoothly from location to location without requiring workers to dismantle parts.
Other elements of a high-quality continuous miner include:
- The ability to navigate around right-angle turns with a small radius
- Enough room to allow for adequate ventilation
- Space to allow miners to install strata supports throughout the mining process
The continuous miner should also have a roof and bolter attached. However, these elements should not prevent construction personnel from placing support pattern rows.
For the most part, continuous miners offer companies high advance rates. However, longwall retreat rates and longwall continuity issues remain a concern for mines that utilize continuous miners.
Developing longwall continuity can strain other service functions, such as personnel, material handling, dust ventilation, water and power supplies, and gas drainage.
Despite these issues, continuous miner systems make coal mining faster while minimizing blasting. In addition, these machines make it possible to meet the increasing demand for underground coal production.
Read on for more information about how companies can use continuous miners to streamline their mining processes while ensuring a safer working environment.
Features and Benefits of Continuous Miners

A continuous miner system includes several critical features that impact the system’s functionality. Generally, these machines operate based on a room-and-pillar system.
Before implementing a continuous mining system, mining companies must divide each mine into 20 to 30 coal beds. Then, workers must install support systems to prevent the mine from collapsing.
After carving work areas into the coal beds, mining teams can begin setting up continuous miners to extract coal. Miners can then carry extracted coal to the surface with the help of a conveyor system.
In many cases, on-site workers operate continuous miners. However, modern continuous miner systems may also feature remote-controlled or robotic features.
Fully automated versions of the mining system make it easier to cut coal in hard-to-mine seams, lowering the risks of operating a continuous miner.
Additional features of the ideal continuous miner include:
A Central Body
The central body of the continuous miner houses all the components mounted on the drive mechanism, including the cutter. It permits mobility during industrial mineral mining applications below the mine roof.
A Cutting Head
The cutting head features a metallic rotating drum. Sharp cutter picks attach to the head and extract coal from the coal seam, working within the machine’s minimum and maximum cutting height.
Some models have a dual gathering head system to increase development rates. Both single and double cutter head systems lift to reach their maximum cutting height. After doing so, internal mechanisms enable the cutters to lower back to their minimum cutting height.
A Loading Mechanism
The loading mechanism harvests the coal and conveys it to a central area within the equipment. Depending upon the automated sequences used by the continuous mining system, the machine may then use conveyors to move coal out of the mine.
A Jib Section
A continuous miner machine typically has a jib at the rear. Operators can move this jib vertically and horizontally during operation. The position of the jib allows for easy coal loading and delivery throughout the system.
Continuous miners typically use one of three room-and-pillar methods to extract coal, as follows.
1. Pillar Splitting
During the pillar splitting process, miners turn roadways created during the initial workings into pillars. Some companies prefer to make pockets instead of full roads.
When using the pillar splitting method, miners must complete their extraction quickly. Due to the stress of mining, the pillars can become unstable.
2. Pillar Stripping
The pillar stripping process requires miners to cut large chunks from the edges of each pillar, forming roadways.
Like the split pillars mentioned above, the standing blocks do not stay stable for long. The efficacy of this process often depends on the minimum cutting height of the continuous miner.
3. Split and Fendering
Throughout the split and rendering process, the roadways leave a six-to-ten-meter fender, or coal strip, between the extracted area and the roadway. After the continuous miner reaches the block limit, the system retreats and returns to the fender.
The miner repeats this process while removing coal from the original panel each time it pulls back. The machine’s traction system provides the power to extract coal, even in compact spaces.
While the split and fendering process is relatively efficient, it presents a substantial risk for on-site personnel. With that in mind, employees should avoid the unsecured roof during the room-and-pillar process.
Transporting Coal While Using a Continuous Miner
Operators must proceed carefully while transporting coal during room-and-pillar mining.
Generally, companies use shuttle cars to carry the mined coal from the extraction point to the transfer point. Machines then tip the coal onto a conveying system connected to the surface.
Tram speed and conveyor width determine how quickly companies can collect and distribute coal to customers.
Narrow conveyor width slows down the process, a factor that companies should consider during the mine construction phase.
Several workers take part in continuous miner operations. Depending upon the situation, you can expect to see a team consisting of:
- An operator for the roof bolts
- A shuttle car operator
- A mechanic to handle tools and mining repairs
- A ventilation miner to assess dust levels and breathability
- A foreman
Team members handle different tools, including the cutter, and keep an eye on the roof for safety reasons during all mining processes. Drivers then deliver each batch of coal to the conveyor.
Pros and Cons of Using a Continuous Miner

Continuous miners provide mining companies with countless benefits. In fact, almost 45% of the coal mined worldwide comes from the efforts of a continuous mining system.
However, there are several potential drawbacks to any mining system. Here, we’ll discuss the pros and cons of continuous mining systems.
Increased Safety
Continuous miner machines provide increased safety in many cases. Some of these systems operate remotely or through the use of robotics.
The systems often offer high advance rates, allowing companies to gather coal without exposing workers to unsafe conditions, high dust levels, or dangerous gases.
Reliability
Companies need reliable machinery for their mining operation sites. With that in mind, continuous miners provide consistent drilling services as long as companies perform regular maintenance on the equipment.
Even so, continuous miners offer high levels of reliability and have a reputation for durability, especially when compared to other mining machinery.
Performance
A continuous miner offers trustworthy support at many coal production sites. Companies often select this system for use in areas where they cannot safely perform longwall mining.
The actual performance of a continuous miner machine depends upon several factors, though, including:
- The dimensions of the pillars in the mine
- The mine’s ventilation scheme
- The company’s haulage system
Each mine uses a unique haulage system and has specific dimensions. However, continuous miner equipment generally functions well, even in close quarters.
Productivity
Despite including “continuous” in the name of a continuous mining system, these machines don’t actually provide constant productivity. While many companies aim for continuous haulage, miners often have to stop or slow down to:
- Navigate corners
- Retreat from one roadway to another
- Steer in the vertical plane
- Wait for shuttle cars to return
Additionally, companies may face equipment delays while workers install roof support systems. Outside of these potential delays, continuous miners allow companies to optimize the operation of their mining facilities.
Electronic and Mechanical Systems
A continuous miner machine uses several different electronic systems. In some cases, these durable systems contain software that enables companies to operate mining equipment remotely.
The operating speed of the software varies by model, though. Some pieces of equipment have older software and systems. These factors may slow down the operating rate of the continuous miner.
Machine Performance Monitoring and Development
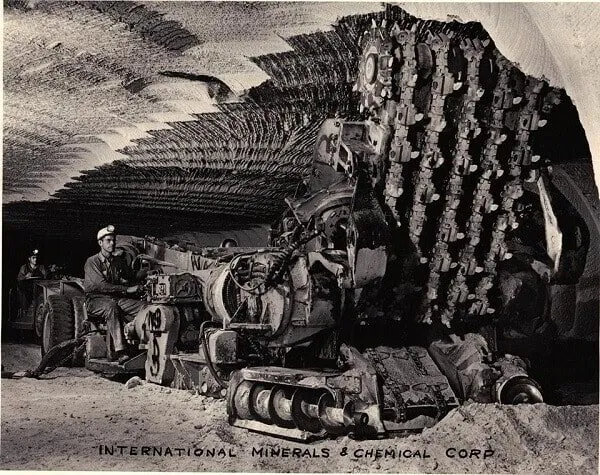
Continuous miner manufacturers focus on furthering the development of new models with increased stability and other benefits.
Many companies, including Komatsu, aim to produce reliable machines with enhanced speed and better remote operations, such as the company’s flagship Joy 12HM31 model.
The Joy 12HM31 features:
- The ability to cut up to 20 tons in a minute
- Dedicated power to traction, cutter, hydraulic, and gathering systems
- Easy outboard access
- Multiple frequencies for radio operations
- A Faceboss control panel
The Joy also provides a cutting width of up to 3,650 millimeters, plus advanced diagnostics thanks to the Optidrive system. In addition, the Joy handles standard width entry applications with ease.
However, Komatsu did not stop development with the Joy range of continuous miners. The company has recently revealed a newer, more advanced machine called the MC51.
Unlike the Joy model, the MC51 has increased functionality for hard rock mining. Previously, companies used continuous miners for underground coal or other soft rock operations.
However, the MC51 goes one step beyond the Joy model’s technological innovations by pioneering hard rock mining, improving mine operations, and protecting workers’ health.
Komastu incorporated suggestions received from companies that used the Joy range when designing the MC51.
As a result, the MC51 aims to surpass the speed goals set by the current models. At the same time, the MC51 version provides increased traction and power.
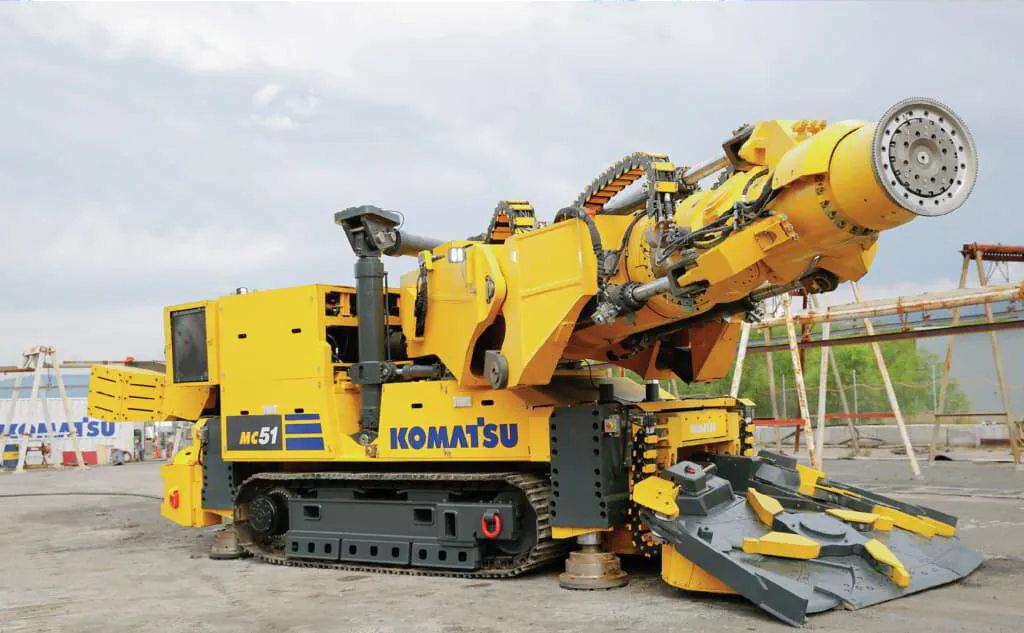